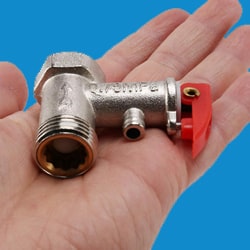
Every year, improperly tested boiler safety valves contribute to increased risks in mechanical engineering environments. Ensuring your valve functions correctly is not just a regulatory requirement; it might prevent catastrophic failures. In this guide, you'll learn the importance of regular safety valve testing, how to prepare for the process, and step-by-step procedures for effective testing. By engaging with this content, you'll empower yourself to mitigate risks associated with faulty relief valves and enhance overall safety in your operations. Let's ensure your equipment meets ASME standards and operates safely.
Introduction to Boiler Safety Valves
boiler safety valves play a critical role in maintaining system integrity by preventing overpressure in applications, including those involving superheaters. You will explore the various types of boiler safety valves and their construction, as well as essential regulatory standards and compliance with the American Society of Mechanical Engineers. This foundation sets the stage for understanding inspection procedures and lever mechanisms crucial to ensuring optimal performance.
Understanding the Purpose of Safety Valves
Understanding the purpose of boiler safety valves is crucial for maintaining the safety and efficiency of any steam or hot water system. These valves are designed to prevent the dangerous buildup of pressure within the boiler, which could lead to catastrophic failures. Regular inspection and testing of these safety valves ensure they function correctly, adhering to the standards set forth by organizations such as the National Board of Boiler and Pressure Vessel Inspectors.
Corrosion is a significant concern when it comes to boiler safety. Over time, the internal components of a safety valve can deteriorate due to exposure to high temperatures and chemical reactions with the water or steam. By understanding the impact of corrosion on safety valves, you can take proactive measures to mitigate risks, ensuring that these vital components operate effectively and safely.
The frequency of testing and inspection of safety valves cannot be overstated. Regular checks help identify any signs of wear or malfunction, which could compromise the boiler's overall safety. You should establish a testing regimen that complies with industry standards and ensures optimal performance, ultimately protecting your system from potential hazards.
- Purpose of safety valves in boiler systems
- Impact of corrosion on valve performance
- Importance of regular testing frequency
Types of Boiler Safety Valves
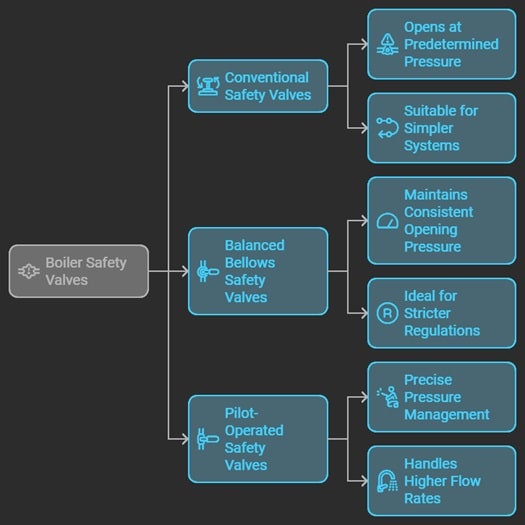
Boiler safety valves are classified into two main types: conventional and balanced bellows safety valves. Conventional safety valves operate by opening when the pressure in the pressure vessel exceeds a predetermined limit. They are widely used in simpler systems where direct pressure monitoring is feasible, making them suitable for many pipe applications.
Balanced bellows safety valves offer improved performance under varying back pressures. These valves contain a mechanism that balances the force exerted by the system pressure, which helps maintain opening pressures regardless of back pressure changes. This design is particularly beneficial for jurisdictions with stricter regulations, ensuring that safety measures are consistently met.
Another type of safety valve commonly utilized is the pilot-operated safety valve, known for its ability to manage higher flow rates. This valve uses a control valve to regulate the opening and closing, allowing for precise pressure management. By understanding the different types of boiler safety valves, you can make better choices regarding maintenance and compliance.
- Conventional safety valves
- Balanced bellows safety valves
- Pilot-operated safety valves
Regulatory Standards and Compliance
Regulatory standards play a crucial role in ensuring that boiler safety valves operate reliably and effectively. Compliance with regulations established by organizations such as the American Society of Mechanical Engineers (ASME) and the National Board of Boiler and Pressure Vessel Inspectors helps maintain safety within facilities using pressure vessels. Understanding these standards means you can ensure that your boiler systems are equipped with the appropriate safety measures, reducing the risk of accidents related to pressure failures.
boiler blowdown practices are another important aspect governed by regulatory standards. Regular blowdown is necessary to remove sediment and prevent corrosion in the tank, but it should be done in compliance with safety regulations to avoid disrupting pressure levels. Familiarizing yourself with these blowdown requirements not only enhances the longevity of your equipment but also ensures that you meet required safety standards.
It's also essential to establish a routine for inspection and testing of your safety valves as mandated by regulatory compliance. Regular checks should include an assessment by certified pressure vessel inspectors to identify any signs of wear or malfunction. By adhering to these requirements, you not only safeguard your boiler system but also demonstrate your commitment to maintaining high safety standards in your operations.
Importance of Regular Safety Valve Testing
Regular testing of boiler safety valves is essential for preventing overpressure incidents, which can lead to severe hazards. Ensuring these valves function properly not only enhances operational efficiency but also meets legal requirements for testing. Topics will cover methods for identifying leaks, the relevance of HVAC Parts in maintaining system integrity, and the critical role of HVAC Supplies in optimizing Radiant Heating and Cooling systems.
Preventing Overpressure Incidents
Preventing overpressure incidents is a critical aspect of boiler safety management. When the pressure within a boiler exceeds safe limits, it can lead to catastrophic failures, risking both personnel safety and property damage. By implementing a routine testing schedule for safety valves, you can ensure that these vital components function correctly, effectively mitigating the dangers associated with excessive pressure buildup.
During your regular safety valve testing, look for signs of wear, leakage, or improper opening pressures. For instance, if a safety valve fails to open when needed, the pressure within the boiler could increase to hazardous levels. Conducting thorough inspections allows you to identify and address potential issues before they escalate into serious incidents, reinforcing the overall safety of your steam or hot water system.
Additionally, being proactive with safety valve maintenance aligns with regulatory compliance standards established by organizations like the American Society of Mechanical Engineers (ASME). Regular testing not only protects your equipment but also ensures you meet legal obligations, providing peace of mind that your boiler systems operate efficiently and safely. By prioritizing these practices, you safeguard your investments while prioritizing the safety of everyone in your facility.
Ensuring Operational Efficiency
Ensuring operational efficiency in your boiler system hinges significantly on the proper functioning of safety valves. When these valves operate effectively, they help prevent overpressure, which can lead to equipment failures and costly downtime. By consistently testing your safety valves, you can confirm their performance and avoid any disruptions that could negatively impact your operations.
In your regular safety valve inspections, focus on identifying any issues that may hinder performance, such as corrosion or improper calibration. An operational safety valve not only protects your equipment but also enhances the overall efficiency of your heating system. This proactive approach not only saves you money in repairs but also contributes to maintaining optimal energy usage.
Ultimately, ensuring operational efficiency through regular testing of boiler safety valves translates to a safer and more productive work environment. By establishing a testing schedule and adhering to regulatory standards, you will not only protect your investments but also enhance the reliability of your steam or hot water system. This commitment to safety and efficiency reinforces your standing as a responsible operator in the industry, ensuring peace of mind for both you and your team.
Legal Requirements for Testing
Legal requirements for testing boiler safety valves are established to ensure equipment safety and operational efficiency. Organizations such as the American Society of Mechanical Engineers (ASME) provide guidelines that dictate the frequency and methods of testing. By adhering to these legal standards, you not only protect your equipment but also ensure the safety of personnel, minimizing liabilities associated with boiler operation.
In many jurisdictions, regulations stipulate that safety valves must undergo regular inspection and testing at specific intervals. This may include annual, semi-annual, or quarterly checks, depending on the type of boiler and its usage. Familiarizing yourself with these requirements is essential to maintain compliance and avoid penalties or operational shutdowns.
To ensure compliance with legal testing requirements, consider developing a detailed testing schedule that aligns with both industry standards and your facility's operational needs. This proactive approach not only safeguards your investment but also reinforces a culture of safety within your organization. By making safety valve testing a priority, you demonstrate your commitment to regulatory compliance and the well-being of your team and operations:
- Understand ASME regulations for boiler safety valves.
- Implement a testing schedule that meets local legal requirements.
- Prioritize safety valve inspections to enhance personnel safety.
Preparing for Safety Valve Testing
Before conducting boiler safety valve testing, you need to gather the necessary tools and equipment, ensuring you have everything at hand for efficient inspections. Safety precautions and personal protective equipment (PPE) are vital for ensuring your safety during the process. Additionally, maintaining accurate documentation and record-keeping is essential to track compliance and performance over time.
Gathering Necessary Tools and Equipment
Gathering the essential tools and equipment for boiler safety valve testing is the first step in ensuring a smooth and effective inspection process. You will need a variety of tools, such as pressure gauges and wrenches, to assess the performance of the safety valves accurately. Having the right equipment on hand not only streamlines the inspection but also helps you identify potential issues before they escalate into hazardous situations.
It's important to include personal protective equipment (PPE) in your toolkit as well. Items like safety goggles, gloves, and protective clothing will shield you from potential hazards when working with high-pressure systems. Prioritizing safety gear is essential to protect yourself while performing safety valve tests, ensuring you can operate with confidence and care.
Additionally, keeping detailed records during testing is crucial for compliance and future reference. A well-organized logbook documenting testing conditions, results, and any maintenance performed on the valves will enhance your ability to track their performance over time. By maintaining accurate records, you can ensure compliance with regulatory standards and make informed decisions regarding maintenance or replacements as needed.
Safety Precautions and Personal Protective Equipment
When preparing for safety valve testing, prioritizing safety precautions is essential. High-pressure systems can pose significant hazards, so it is vital to conduct a risk assessment before beginning your inspections. By understanding the potential dangers, you can formulate a plan that minimizes risks during the testing process.
Personal protective equipment (PPE) plays a critical role in ensuring your safety while working with boiler systems. Always wear appropriate safety goggles to shield your eyes from potential splashes or debris, along with gloves to protect your hands from high temperatures and sharp edges. Additionally, consider using protective clothing that covers your arms and legs, reducing the risk of injury in the event of an accident.
Establishing a clear protocol for safety precautions will help keep you and your team safe during testing. Ensure that everyone involved in the process understands the importance of using PPE and follows established safety guidelines diligently. To support this, you may want to review the following important steps for safety during testing:
- Conduct a thorough risk assessment of the boiler system.
- Wear appropriate PPE, including goggles, gloves, and protective clothing.
- Communicate safety protocols clearly with your team.
Documentation and Record-Keeping
Maintaining accurate documentation is essential when preparing for boiler safety valve testing. Proper records help you track the performance of your valves over time and ensure compliance with industry regulations. Documenting testing conditions, results, and any maintenance performed on the valves allows you to identify patterns or issues that may require attention.
When conducting tests, always make sure to record critical information such as the date, time, and conditions under which the testing occurred. This data serves not only for your internal monitoring but also can be crucial during inspections by certified pressure vessel inspectors. Keeping clear and organized records helps instill confidence in your procedures and demonstrates compliance with standards set forth by organizations like ASME.
The use of a well-maintained logbook can greatly benefit your operation. It provides a detailed history of your safety valve inspections, making it easier to assess performance metrics or identify recurring problems. By prioritizing thorough documentation, you can enhance safety, support your team's efficiency, and promote a proactive approach to maintenance that ultimately safeguards your boiler system.
Step-by-Step Guide to Testing Boiler Safety Valves
Testing boiler safety valves involves a series of critical steps, ensuring your system operates safely and efficiently. This guide will instruct you on isolating and depressurizing the boiler, performing a visual inspection of the valve, conducting a manual lift test, and running a set pressure test. Finally, you will learn how to properly reassemble and re-pressurize the boiler, keeping your operations compliant and risk-free.
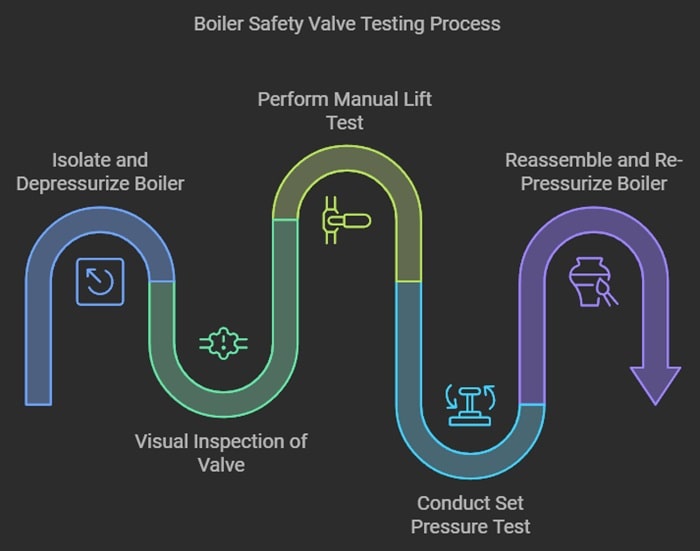
Isolating and Depressurizing the boiler
Isolating and depressurizing the boiler is the first critical step in testing your safety valves. You should begin by shutting down the boiler system according to the manufacturer's guidelines. This process often involves closing the fuel supply and ensuring electrical systems are safely powered down to prevent any accidental start-up during your inspection.
Once the boiler is turned off, you will need to isolate it from the rest of the system. This typically requires shutting the inlet and outlet valves connecting the boiler to the piping system. By doing this, you effectively create a safe environment for testing, eliminating the risk of pressure fluctuations that could lead to dangerous scenarios.
After isolating the boiler, proceed to depressurize it fully. Make sure that you open the vents or drain valves on the boiler to allow steam or water to escape safely. This method will help you confirm that the system pressure is at a safe level for inspection, ensuring that you can test the safety valves without risk of overpressure incidents:
- Shut down the boiler system according to guidelines.
- Isolate the boiler by closing the inlet and outlet valves.
- Depressurize the boiler by opening vents or drain valves.
Visual Inspection of the Valve
Performing a visual inspection of the boiler safety valve is essential to ensure its proper operation and safety. Start by checking for any signs of leakage, damage, or corrosion on the valve body and surrounding connections. This examination helps in identifying potential issues before they escalate into serious problems, allowing you to take corrective actions promptly.
Next, examine the valve’s components for any visible wear. Look for debris or foreign materials that may hinder the valve's ability to open and close effectively. A thorough inspection not only confirms the physical integrity of the valve but also provides insight into the overall condition of your boiler system, ensuring optimal performance.
Finally, confirm that the valve is securely mounted and all fasteners are tight. A loose valve can lead to malfunctions and pressure inconsistencies, impacting the safety of your entire system. By addressing these factors during your visual inspection, you can enhance the reliability and efficiency of your boiler safety valve:
- Check for signs of leakage and corrosion.
- Examine components for physical wear.
- Ensure the valve is securely mounted and the fasteners are tight.
Performing the Manual Lift Test
The manual lift test is an essential procedure to ensure the proper functionality of your boiler safety valves. To perform this test, you will gently lift the valve bonnet to simulate the operating conditions when the valve opens under excess pressure. This hands-on approach allows you to verify that the valve responds appropriately, confirming its reliability in preventing overpressure situations.
As you conduct the manual lift test, pay close attention to the valve’s performance. Observe whether it opens smoothly and closes fully once released. Any hesitance or failure to close can indicate issues such as wear or buildup that need immediate attention, ensuring that the boiler system remains secure and operational.
Performing the manual lift test also allows you to assess the overall condition of the safety valve in real-time. If you identify any irregularities during this test, it is advisable to document your findings and take corrective actions promptly. Regular execution of this test reinforces the safety and efficiency of your boiler systems, preventing potential hazards down the line.
Conducting the Set Pressure Test
Conducting the set pressure test is a critical component of ensuring your boiler safety valves function properly. To perform this test, you'll first need to configure the testing setup according to the manufacturer's specifications to accurately monitor pressure levels. By applying pressure gradually, you can determine at what point the safety valve opens, thus confirming its effectiveness in preventing overpressure conditions in your system.
During the set pressure test, pay attention to the reading on your pressure gauge to ensure it aligns with the safety valve's designated set point. If the valve opens at the correct pressure, it indicates that the safety mechanism is operational. However, should the valve open too early or too late, you may need to recalibrate or replace it to maintain system integrity.
This testing procedure also allows you to verify the valve's closing performance. Once the pressure is relieved, ensure the valve closes promptly and seals completely. A valve that fails to close correctly may lead to continuous pressure loss, risking both efficiency and safety in your boiler system. By regularly conducting the set pressure test, you enhance the reliability of your boiler and protect against potential hazards from pressure fluctuations.
Reassembling and Re-Pressurizing the boiler
Once you have completed the necessary testing on the boiler safety valves, the next step is reassembling and re-pressurizing the boiler system. Begin by securely reattaching the safety valve and ensuring that all bolts and fittings are tight. This step is vital to prevent any leaks that could compromise the integrity of your boiler system after testing.
After reassembling, you can begin the re-pressurization process. Gradually open the boiler's inlet and outlet valves to allow water or steam to enter while carefully monitoring the pressure gauge. This allows you to confirm that the pressure is increasing steadily and that the safety valve functions as intended without any unexpected fluctuations.
Finally, once the system reaches the required operational pressure, a final inspection for any leaks or irregularities is performed. If everything operates smoothly, document the testing and inspection results to maintain compliance with regulatory standards. Keeping accurate records helps ensure the ongoing reliability of your boiler system and demonstrates your commitment to safety and efficiency:
- Securely reattach the safety valve.
- Gradually re-pressurize the boiler system.
- Monitor for leaks and ensure smooth operation.
Common Issues and Troubleshooting
Identifying signs of valve wear or damage is crucial for maintaining the integrity of your boiler system. You should be alert for any leakage and steam loss, as these issues can significantly impact performance. When it comes to repair or replacement, knowing when to act can prevent safety hazards. Understanding these common problems will empower you to ensure your safety valves operate efficiently and reliably.
Identifying Signs of Valve Wear or Damage
When assessing boiler safety valves, look for any signs of leakage around the valve body and connections. Leaks can indicate a compromised seal that may prevent the valve from operating correctly, which poses risks for overpressure situations. By routinely inspecting these areas, you can identify potential issues before they escalate into more serious problems.
Additionally, keep an eye out for any unusual noises during operation, such as hissing or rattling sounds. These noises may suggest internal wear of the valve components or debris that could impact its performance. Addressing these irregularities promptly can help maintain the valve's reliability and ensure ongoing safety in your boiler system.
Lastly, check for visible corrosion or wear on the valve body and actuator. Corrosion can indicate prolonged exposure to moisture or chemicals that compromise the valve's integrity. If you notice significant deterioration, consider scheduling a repair or replacement to uphold the safety standards for your boiler system and avoid unnecessary downtime.
Addressing Leakage and Steam Loss
Addressing leakage in boiler safety valves is essential for maintaining system integrity and operational efficiency. An early indication of leakage may include noticeable drops in pressure or visible water seeping around the valve body. By frequently inspecting these areas, you can catch issues before they escalate into larger problems that threaten your boiler's performance.
Steam loss represents another significant concern, as it can lead to wasted energy and increased operational costs. If you observe hissing sounds or steam escaping from the valve, this could signal a malfunction. Taking prompt corrective action, such as tightening fittings or replacing worn components, can help restore proper function and efficiency in your boiler system.
To effectively manage leakage and steam loss, establishing a regular maintenance schedule is key. This proactive approach not only helps you identify issues early on but can also extend the life of your equipment. Regular inspections and timely repairs safeguard both your investment and workplace safety:
- Regularly inspect for leaks around valves and connections.
- Identify and correct steam loss as soon as possible.
- Implement a maintenance schedule for ongoing performance and safety.
When to Repair or Replace a Safety Valve
Determining when to repair or replace a safety valve involves assessing its overall condition and performance. If you notice signs of leakage, persistent steam loss, or irregular noises during operation, these issues may indicate that the valve is no longer functioning properly. In such cases, taking prompt action—whether through repair or replacement—ensures the continued safety and efficiency of your boiler system.
An essential factor to consider is the age of the safety valve. Even if a valve appears to function correctly, older valves may be subject to wear and corrosion that compromise their reliability. Regular inspections can reveal whether your valve has reached the end of its useful life, allowing you to make informed decisions about repairs versus replacements before any critical failures occur.
Ultimately, understanding the balance between repair costs and replacement expenses is crucial in your decision-making process. If the repairs are frequent and costly, it may be more prudent to invest in a new safety valve to ensure reliable operation and compliance with safety standards. This proactive approach not only protects your investment but also enhances the overall performance of your boiler system, safeguarding against unexpected downtime or accidents.
Best Practices for Ongoing Maintenance
Establishing a regular testing schedule for boiler safety valves is vital for ongoing maintenance. You should also prioritize training your staff on essential safety procedures to promote a safer work environment. Furthermore, collaborating with certified inspectors enhances the reliability of your safety systems. Each of these strategies plays a crucial role in maintaining optimal performance and compliance.
Establishing a Regular Testing Schedule
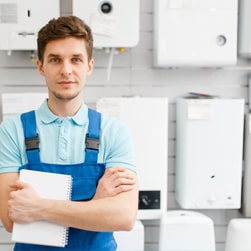
Establishing a regular testing schedule for boiler safety valves is essential for maintaining the safety and efficiency of your steam or hot water system. Determine the appropriate intervals for testing by considering factors such as the type of boiler, its usage, and applicable regulatory requirements. By customizing your schedule to your specific needs, you can ensure that your safety valves are routinely checked to prevent overpressure incidents.
Incorporate your established testing schedule into your organization's standard operating procedures to ensure consistency. Make this schedule accessible to all relevant personnel, enabling them to be aware of testing dates and responsibilities. By fostering a culture of accountability, you can enhance the reliability of your boiler system and demonstrate your commitment to safety.
Regular testing not only helps you identify potential issues early but also aligns your operations with legal requirements set by authorities like the American Society of Mechanical Engineers (ASME). Keep detailed records of each testing session, including outcomes and any required maintenance, to provide transparency and support compliance efforts. This proactive approach not only safeguards your equipment but also gives you peace of mind, knowing that your boiler safety valves are functioning correctly.
Training Staff on Safety Procedures
Training your staff on safety procedures is essential for the effective operation and maintenance of boiler safety valves. Ensure that team members fully understand the critical importance of these valves in preventing overpressure incidents, as their correct usage can significantly reduce risks. Consider conducting regular training sessions that focus on safety protocols, testing techniques, and emergency response strategies to empower your staff with the knowledge they need to act effectively.
Incorporating hands-on training into your program allows staff to engage directly with boiler safety valves and testing equipment. Practical demonstrations can help reinforce procedures, ensuring that everyone can confidently perform inspections and identify any signs of wear or damage. This interactive approach not only builds skills but also fosters a culture of safety and accountability within your organization.
Furthermore, maintaining an open line of communication encourages staff to share insights and experiences related to safety valve operations. Regularly scheduled meetings can serve as a platform for discussing challenges, updates on industry standards, and regulatory changes. By fostering a collaborative learning environment, you’ll enhance your team's overall competence in managing boiler safety valves, ultimately ensuring compliance and the safety of your operations.
Collaborating With Certified Inspectors
Collaborating with certified inspectors is vital for ensuring the safety and efficiency of your boiler safety valves. These professionals bring expertise and familiarity with industry standards, allowing them to perform thorough evaluations of your systems. By engaging certified inspectors, you can identify potential vulnerabilities in your safety mechanisms, thus reinforcing the reliability of your operations.
Regular input from certified inspectors enhances your compliance with regulations set forth by organizations like the American Society of Mechanical Engineers. They can assess your boiler and safety valve performance, providing insights that help you maintain a sturdy safety regimen. This partnership not only promotes adherence to legal requirements but also builds a proactive maintenance culture that prioritizes safety and efficiency.
In addition, certified inspectors can offer tailored recommendations for testing and maintenance schedules suited to your specific needs. Their professional guidance enables you to make informed decisions about repairs and upgrades, ensuring your safety valves maintain optimal performance. By fostering a relationship with these experts, you can protect your investment and enhance the overall safety of your boiler systems.
Conclusion
Effective boiler safety valve testing is essential for preventing overpressure incidents and ensuring the safe operation of steam and hot water systems. Regular inspections, including visual checks, manual lift tests, and set pressure tests, empower you to identify issues before they escalate into serious hazards. By adhering to regulatory standards and establishing comprehensive testing procedures, you enhance both efficiency and safety while demonstrating your commitment to equipment reliability. Prioritize these practices to protect your investment and foster a safe working environment for everyone involved.
Resources:
Learn about HVAC
Learn about boilers